Fluxing Tank Reprocessing & Regenerating System
Product Description
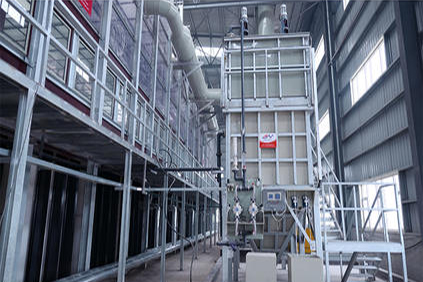
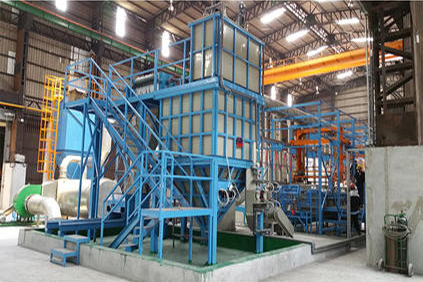
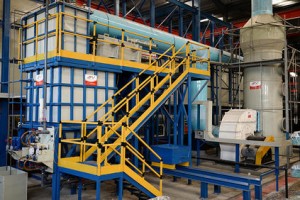
The fluxing bath is being polluted by acid residues and above all by dissolved iron in Hot galvanizing plant . Consequently it makes the quality of the galvanizing process worse; moreover iron being entered by a polluted fluxing flow into the galvanizing bath binds itself with zinc and precipitates to the bottom, thus increasing dross.
A continuous treatment of the fluxing bath will help you get rid of this problem and cut the zinc consumption dramatically.
The continuous depuration is based upon two combined reactions an acid-base reaction and an oxide reduction which correct fluxing acidity and simultaneously cause the iron to precipitate.
The mud collected at the bottom is regularly being tapped and filtered.
to continuously abate iron in the flux by adding suitable reagents in the tank, while a separate filter press extracts the oxidized iron on line. A good design of the filter press allows to extract iron without intercepting the indispensable Ammonium and Zinc Chlorides used in flux solutions. Managing the iron abatement system also allows to keep ammonium and zinc chloride contents under control and suitable balanced.
Flux regeneration and filter press systems plant are dependable, easy to use and to maintain, so much so that even inexperienced operators will be able to handle them.
Features
-
- Flux treated in continuous cycle.
- Fully automatic system with PLC controls.
- Convert Fe2+ into Fe3+ to sludge.
- Control of flux process parameters.
- Filter system for the sludge.
- Dosing pumps with pH & ORP controls.
- Probes attached with pH & ORP transmitters
- Mixer for dissolving reagent.
Benefits
-
-
- Reduces zinc consumption.
- Minimizes the transfer of iron to molten zinc.
- Reduces ash and dross generation.
- Flux operates with at a low iron concentration.
- Iron removal from solution during production.
- Lowers flux consumption.
- No black spots or Zn Ash residues on the galvanized piece.
- Ensures product quality.
-