Materials Handling Equipment
Product Description
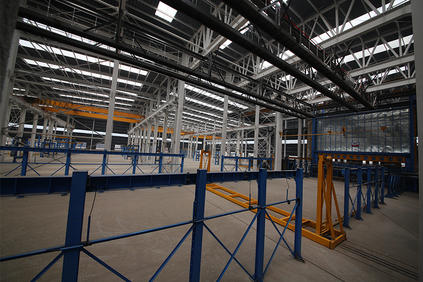
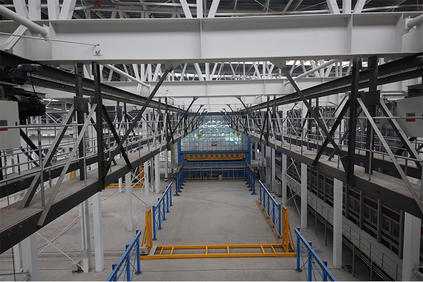
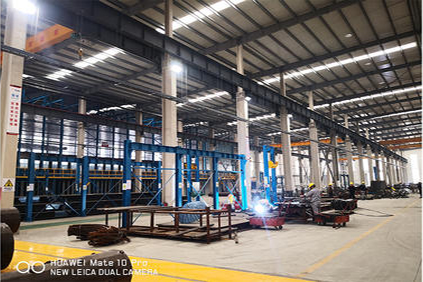
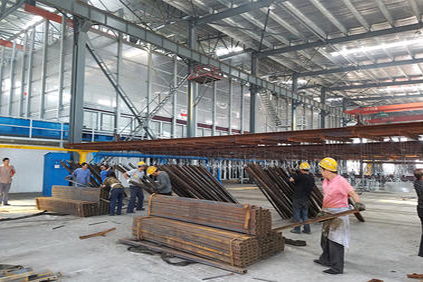
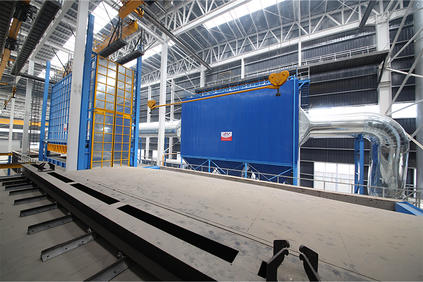
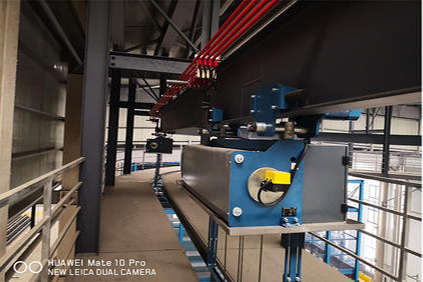
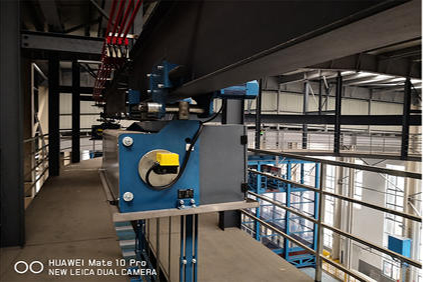

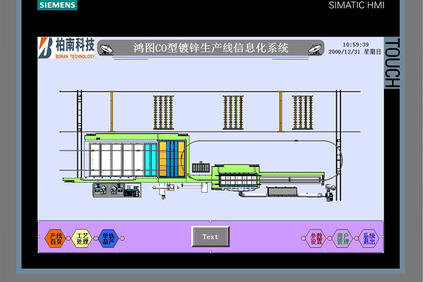
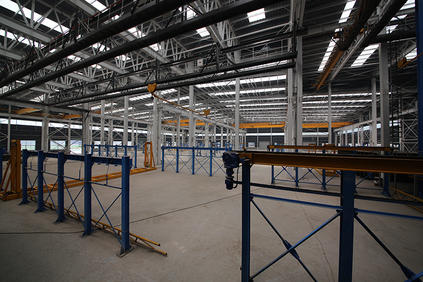

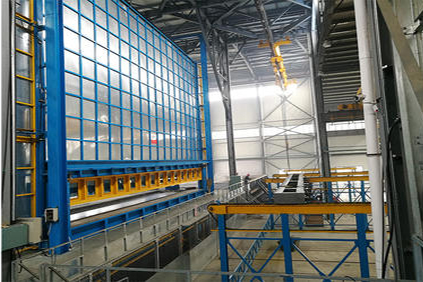
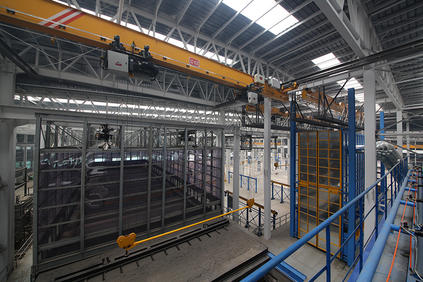
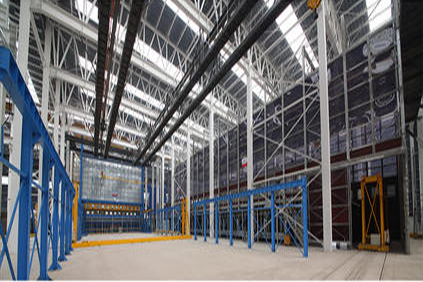
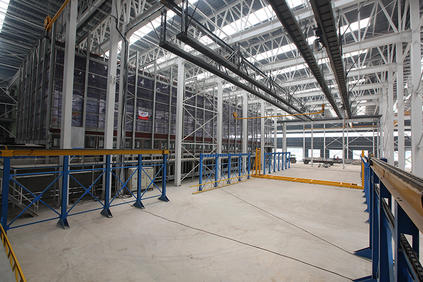
- A fully automatic transmission device for hot galvanizing processing, belonging to the field of hot galvanizing processing, comprises a base, a conveyor belt is installed in the middle of the upper surface of the base, a plurality of positioning rods are installed on the surface of the conveyor belt along the length direction, a cooling box is fixed on one side of the upper surface of the base, a blanking plate is fixed on one side of the upper surface of the cooling box through a fixing rod, and two pillars are symmetrically installed on the other side of the lower surface of the base, A rotating shaft is installed between two pillars, and a cylinder is fixed on the rotating shaft. The cylinder is a cylindrical structure. Four transfer grooves are arranged along the circumference array on the side wall of the cylinder, and both ends of the transfer grooves are fixed with screens. A blanking box is fixed between two pillars, and the blanking box is located right above the cylinder; The utility model is novel in design. During the transportation of hot-dip galvanized steel pipes, the steel pipes are efficiently air-cooled and water-cooled to ensure the cooling effect. The subsequent processing is used to improve the product quality, which is worth popularizing
Product Details
Generally speaking, it can be used for hot water making, process heating, cooling and drying. The computer group can be configured only after understanding the waste heat and recycling the heat of the new process. When the waste heat can meet the heat energy demand of the new process, the waste heat recovery device can be directly used for heat exchange. When the waste heat cannot meet the heat energy demand of the new process, the waste heat can be used for preheating, and the insufficient heat can be supplemented by heat pump equipment, or the existing heating equipment.
In either case, the energy saving effect is much more obvious than that of the original waste heat, so as to achieve the purpose of reducing energy consumption and improving efficiency.
After the waste heat recovery from the flue gas preheating of the galvanizing line, it can be used for the hot water demand and the heating of various solutions in the pre-treatment and post-treatment processes of hot galvanizing. Customized waste heat recovery heat exchanger has high heat exchange efficiency, touch-screen operation control, and can be connected to a computer or mobile phone for easy management, saving enterprises tens of thousands to hundreds of thousands each year.
Waste heat recovery depends on heat exchanger, but system design is more important. The whole set of waste heat recovery project can only be completed if the type, temperature, and heat of the enterprise's waste heat are well prepared in advance, and the production conditions, process flow, internal and external energy demand, etc. are investigated.