Hot-dip galvanizing is a widely used method for protecting steel and iron from corrosion. This process involves immersing the metal in a bath of molten zinc, which forms a robust, protective coating. The resulting galvanized metal is highly resistant to rust and can withstand harsh environmental conditions. However, achieving optimal results requires adherence to specific requirements and best practices. This article delves into the essential requirements for hot-dip galvanizing to ensure high-quality and durable outcomes.
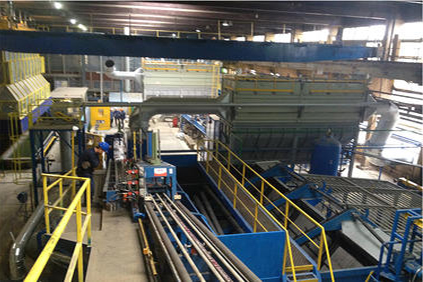

1. Material Selection
The first requirement for hot-dip galvanizing is the selection of appropriate materials. Not all metals are suitable for this process. Typically, steel and iron are the primary candidates. The composition of the metal can significantly affect the quality of the galvanizing. For instance, the presence of elements like silicon and phosphorus in steel can influence the thickness and appearance of the zinc coating. Therefore, it is crucial to choose materials with controlled and known compositions to achieve consistent results.
2. Surface Preparation
Surface preparation is a critical step in the hot-dip galvanizing process. The metal surface must be clean and free from contaminants such as oil, grease, rust, and mill scale. Any impurities can prevent the zinc from adhering properly, leading to poor coating quality. The surface preparation typically involves three stages:
- Degreasing: Removal of organic contaminants using alkaline solutions or solvents.
- Pickling: Removal of rust and scale using acidic solutions, usually hydrochloric or sulfuric acid.
- Fluxing: Application of a flux solution, often zinc ammonium chloride, to prevent oxidation before immersion in the molten zinc.
Proper surface preparation ensures a strong bond between the metal and the zinc coating, enhancing the durability and effectiveness of the galvanizing.
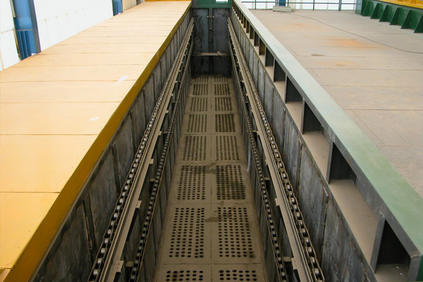
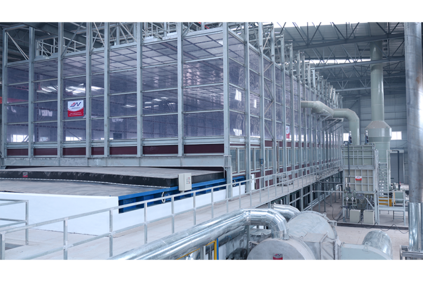
3. Bath Composition and Temperature
The composition and temperature of the zinc bath are crucial factors in the hot-dip galvanizing process. The zinc bath should contain at least 98% pure zinc, with the remaining percentage comprising elements like aluminum, lead, and antimony to improve the coating’s properties. The bath temperature typically ranges between 820°F and 860°F (438°C to 460°C). Maintaining the correct temperature is essential for achieving a uniform and high-quality coating. Deviations can result in defects such as uneven thickness, poor adhesion, and surface roughness.
4. Immersion Time
The immersion time in the zinc bath is another critical parameter. It depends on the thickness and size of the metal being galvanized. Generally, the metal is immersed until it reaches the bath temperature, allowing the zinc to form a metallurgical bond with the steel. Over-immersion can lead to excessive coating thickness, while under-immersion can result in inadequate protection. Therefore, precise control of immersion time is necessary to achieve the desired coating thickness and quality.
5. Post-Galvanizing Treatment
After the metal is removed from the zinc bath, it undergoes post-galvanizing treatments to enhance the coating’s properties. These treatments may include quenching in water or air cooling to solidify the zinc coating quickly. Additionally, passivation treatments can be applied to prevent the formation of white rust, a type of corrosion that can occur on freshly galvanized surfaces. Proper handling and storage of galvanized materials are also essential to maintain the coating’s integrity.
6. Inspection and Quality Control
Finally, thorough inspection and quality control are vital to ensure the success of the hot-dip galvanizing process. Inspections typically involve visual assessments, thickness measurements, and adhesion tests. Standards such as ASTM A123/A123M provide guidelines for acceptable coating thickness and quality. Adhering to these standards ensures that the galvanized products meet the required performance criteria and provide long-lasting protection against corrosion.
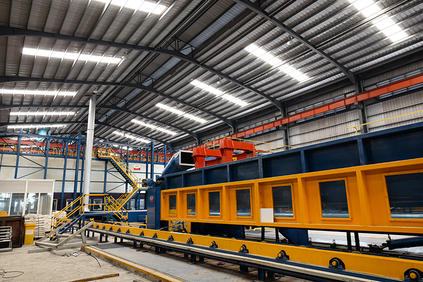
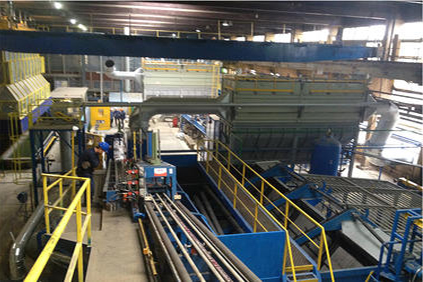
Conclusion
Hot-dip galvanizing is an effective method for protecting steel and iron from corrosion, but it requires meticulous attention to detail and adherence to specific requirements. From material selection and surface preparation to bath composition, immersion time, and post-galvanizing treatments, each step plays a crucial role in achieving high-quality and durable galvanized coatings. By following these best practices and maintaining rigorous quality control, manufacturers can ensure that their galvanized products deliver optimal performance and longevity.
Post time: Sep-18-2024