Galvanizing is a crucial process in the metal industry, primarily used to protect steel and iron from corrosion. By applying a protective zinc coating, galvanizing extends the lifespan of metal products, making them more durable and suitable for various applications. There are three primary methods of galvanizing: hot-dip galvanizing, electro-galvanizing, and zinc spraying. Each method has its unique processes, advantages, and applications, which we will explore in detail, including the roles of galvanizing lines, drying pits, and fluxing tank reprocessing in these methods.
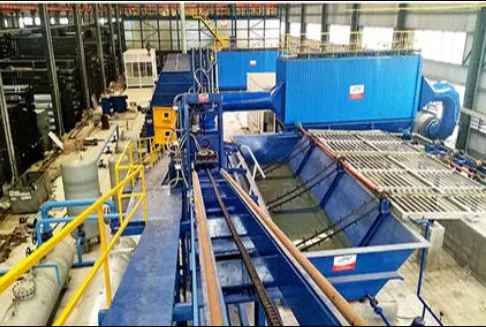
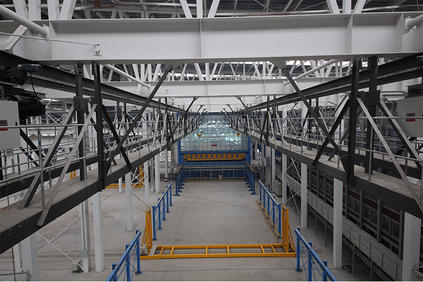
1. Hot-Dip Galvanizing
Hot-dip galvanizing is the most widely used method of galvanizing. In this process, steel or iron parts are submerged in a bath of molten zinc at temperatures around 450°C (842°F). The process begins with surface preparation, which is critical for ensuring a strong bond between the zinc and the metal. This preparation typically involves cleaning the metal to remove any rust, oil, or contaminants, often using a combination of mechanical and chemical methods.
Once the surface is prepared, the metal is dipped into the molten zinc. The heat from the molten zinc causes a metallurgical reaction, forming a series of zinc-iron alloy layers that bond tightly to the steel substrate. After the dipping process, the galvanized parts are removed and allowed to cool, during which the zinc solidifies and forms a protective coating.
Role of Galvanizing Lines: In hot-dip galvanizing, galvanizing lines are essential. These lines are specialized production setups that streamline the entire galvanizing process, from surface preparation to the final cooling stage. They often include automated systems for cleaning, fluxing, and dipping, ensuring efficiency and consistency in the coating process.
Drying Pit: After the cleaning process, the metal parts are often placed in a drying pit. This step is crucial as it ensures that any residual moisture is removed before the parts are dipped into the molten zinc. A well-maintained drying pit helps prevent defects in the galvanizing process, such as zinc adhesion issues or uneven coating.
2. Electro-Galvanizing
Electro-galvanizing, or electroplating, is another method of applying a zinc coating to steel. Unlike hot-dip galvanizing, this process uses an electrolytic solution containing zinc salts. The metal parts are submerged in this solution and connected to a power source, which causes zinc ions to migrate and deposit onto the surface of the metal.
The electro-galvanizing process allows for a thinner and more uniform coating compared to hot-dip galvanizing. This method is particularly advantageous for applications where a smooth finish is required, such as in automotive parts or appliances. However, the coating is generally less durable than that produced by hot-dip galvanizing, making it more suitable for indoor applications or environments with less exposure to corrosive elements.
Fluxing Tank Reprocessing: In electro-galvanizing, fluxing tank reprocessing plays a vital role. Fluxing agents are used to prepare the surface of the metal and enhance the adhesion of the zinc coating. After the electro-galvanizing process, the fluxing solution may need to be reprocessed to maintain its effectiveness and ensure consistent results. This involves filtering and replenishing the fluxing agents to optimize the coating process.
3. Zinc Spraying
Zinc spraying, also known as thermal spraying or metallizing, is a method that involves spraying molten zinc onto the surface of the metal. This process can be performed using various techniques, including flame spraying or arc spraying. In flame spraying, a mixture of zinc powder and oxygen is ignited, creating a flame that melts the zinc and propels it onto the substrate. In arc spraying, an electric arc melts the zinc wire, which is then sprayed onto the surface.
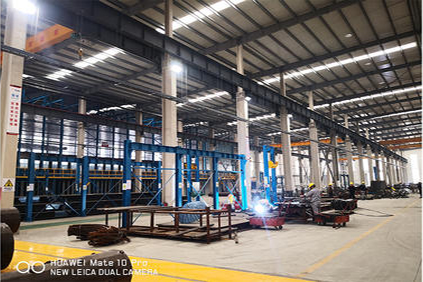
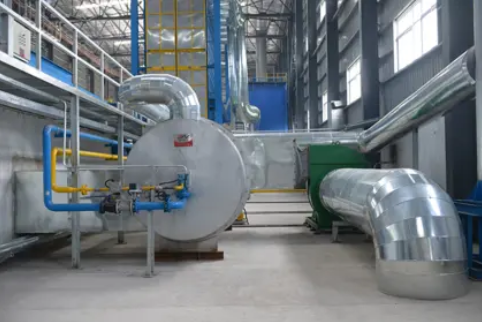
Zinc spraying is particularly useful for large structures or components that cannot be easily dipped into molten zinc. It provides a flexible solution for protecting surfaces that may be difficult to galvanize using traditional methods. However, the coating produced by zinc spraying is generally thicker and may require additional finishing processes to achieve a smooth surface.
Applications and Considerations: Each galvanizing method has its specific applications and considerations. Hot-dip galvanizing is ideal for outdoor structures, such as bridges and utility poles, where long-term corrosion resistance is critical. Electro-galvanizing is often used in automotive and appliance manufacturing, where aesthetics and smooth finishes are essential. Zinc spraying is suitable for large or complex components, such as ship hulls or industrial machinery.
In conclusion, the three methods of galvanizing—hot-dip galvanizing, electro-galvanizing, and zinc spraying—each offer unique advantages and applications. The processes involved, including the use of galvanizing lines, drying pits, and fluxing tank reprocessing, play a significant role in ensuring the quality and effectiveness of the zinc coating. Understanding these methods allows manufacturers to choose the most appropriate galvanizing technique for their specific needs, ultimately enhancing the durability and longevity of metal products.
Post time: Feb-26-2025